フィギュアリングとは
溶接方法の中で、溶化材(溶接棒等)を使用する溶接には、プラズマ溶接、TIG溶接、MIG溶接など、様々な種類があるが、一般に材料(肉)を供給しながら溶接を行なうので肉盛溶接とも呼ばれている。
母材同士を溶融させることに比べれば、熱影響が少なく、使用エネルギーが少ない、難材質や異種金属接合が可能などのメリットが ある。
また、金属製品の磨耗、欠損、改造などに、肉盛溶接を使用されることが非常に多い。
この肉盛溶接と、レーザの高エネルギー、高精度を利用し、精密な金属部品や金型を再生する技術をレーザフィギュアリングという。
従来の再生方法
従来、様々な製品を再生、もしくは補修する方法として、溶接、メッキ、電着、溶射などがあるが、最も多く使われているのが溶接棒を使ったTIG溶接である。
TIG溶接による肉盛
メリットとしては、機械が安価であり、溶接棒の種類が豊富であるなどが挙げられるが、精密な製品では熱入力が過大になり変形や歪みを起こす。
トーチを操作するので、奥まった箇所には対応出来ない。
また、手作業の為に作業者の熟練度が品質に大きな影響を及ぼす。
TIG溶接による肉盛(考察)
実際にTIG溶接機を使用して、以下の条件で肉盛溶接を行なった。
(写真1)は、TIG溶接機で肉盛溶接を行なった、外観写真である。ワーク全体が大きく焼けており、熱入力が過大であるのがわかる。
作業においてもコントロールが難しく、タングステン電極の先端の状態や、角度、電極とワークとの距離、送りスピードの違いにより、ビート幅、溶け込み量(盛量)、入熱量など、様々な要素に変化が生じる。
この為に、安定した加工が得られず、今日では職人技任せという現状である。

(写真2)は写真1赤丸部分の拡大写真である。
ワークと溶接材との境界に、幅約1mm程のへこみが発生している。一般にヒケやアンダーカットと呼ばれて
いるが、金属が溶融し凝固する時に、ワークが溶接材に引っ張られて起こる現象である。
この現象が更に拡大すると、割れやクラックが発生する。
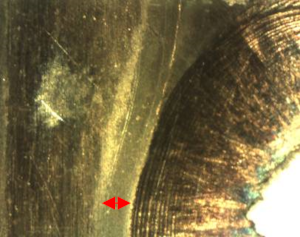
(写真3)は断面写真である。熱影響部分が大きい事がわかる。ワークと溶接材との境界に、深さ方向に0.05mmのアンダーカットが発生している。
また、溶接材部分は組成変化を起こし、ワークの硬度も低下している。
NAK80の硬度は約HRC40に対して、溶接材部分はHRC32であった。
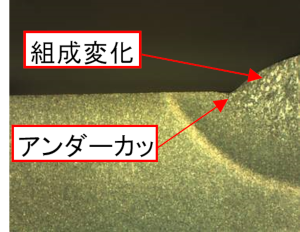
精密な部品や、高精度の金型などに肉盛溶接を施す場合、従来のTIG溶接では、熱入力が大きいことや、作業条件の不安定性などから、変形、クラック、組成変形アンダーカット、ピンホールなど、様々な問題が生じる。
フィギュアリング
レーザ加工の特徴は、高エネルギーを高密度に非接触で、微細コントロール出来る点である。
フィギュアリングにおいても、微細な部分に必要最小限の熱エネルギーをコントロールする事により、熱歪みや、アンダーカット、ポロシティや、クラックの無い溶接を行なうことが可能である。
1. 次のようなフィギュアリングを行なった。
試験材料
材質 NAK80 寸法 22×15×t15mm
溶接棒(ワイヤー) NAK80 φ0.3mm
溶接ビート幅 0.7mm
使用機械
パルス発振式YAGレーザ120W
(写真4)は、スポット径をφ0.7mmに設定して、φ0.3mmのNAK80溶接ワイヤーをパルス照射して、フィギュアリングを行なった。
酸化防止の為にシールドガスとしてアルゴンを使用した。
熱影響が殆ど無い為に、焼けが無くアンダーカットも見られない。
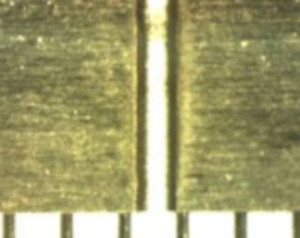
(写真5)は、断面写真である。溶接材がワークへ十分溶け込んでいることから、高い溶接強度を有している。
また、アンダーカット、ポロシティ、クラックなども発生していない。
溶接材部分の硬度もHRC41とワークとほぼ同等であった。

(写真6)は溶接ビートを積み重ねて、面形状にフィギュアリングした外観写真である。
ワーク全体に対する熱入力は大幅に増えたが、焼けやアンダーカットなどは見られない。

(写真7)は溶接ビートを積み重ねたフィギュアリングの断面写真である。
面形状のフィギュアリングを3段重ねている。
焼けやアンダーカットは見られず、クラックやポロシティの発生も無かった。
溶接材部分上面の硬度を測定しHRC39とワークとほぼ同等の硬度であった。
フィギュアリングの厚みは、ワークより+0.55mmである。

2. 次に材料を変更して同様のフィギュアリングを行なった。
材質 SKD11
溶接棒 SKD11 φ0.3mm
溶接ビート幅 0.7mm
(写真8)はスポット径をφ0.7mmに設定して、φ0.3mmのSKD11の溶接ワイヤーをパルス照射して、フィギュアリングを行なった断面写真である。
また、同様に(写真9)は溶接ビートを積み重ねて、面形状にフィギュアリングした断面写真である。
どちらも焼け、クラック、ポロシティ、熱歪みなどは見られず、良好なフィギュアリングを行なうことが出来た。

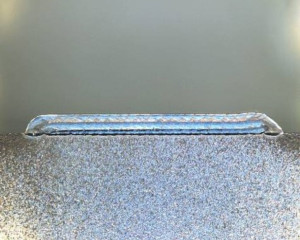
尚、高硬度材にフィギュアリングを行なった場合、レーザ溶接の特徴である、急速加熱、急速冷却の溶融凝固形態を取る為に、同時に焼き入れを行なえるのも利点の一つである。但し、温度や冷却時間を管理できない為に、任意の硬度設定を行なうことは出来ない。
また特に高硬度材においては、条件によりマイクロクラックが発生する場合がある。
対処方法としては、熱入力の調整、加工スピードの減速、パルスの波形制御、予熱処理などを行なうとマイクロクラック発生を抑えることが可能である。
レーザフィギュアリング事例
レーザの特徴を活かした、様々な事例を紹介する。
1. 工具成型品バリ止めの為、パーティングラインをレーザフィギュアリング
(写真10)は工具成型の金型である。パーティングラインの磨耗により、成型品にバリが発生した。
また、製品面にはシボ加工が施してあり、溶接材がシボ加工面に付くと、後工程に大幅な時間とコストが発生してしまう。
(写真11)は、フィギュアリング後の写真である。
幅0.8mmのビートで、シボ加工面かかる事無くポイントのみにフィギュアリングが出来ているので後加工が大幅に短縮出来た。
(ワーク NAK80 溶接材 NAK80)
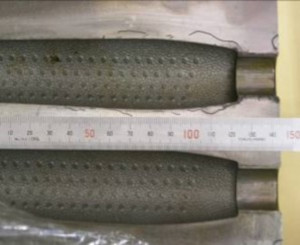
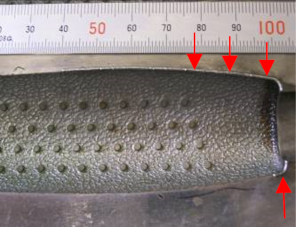
2. 複雑形状のフィギュアリング
(写真12)は電子部品の金型である。形状変更の為に、指示部を0.3mm厚みを増やさなければいけない。
周りにはボスや穴があるので、これらに影響を与えない加工が必要であった。
熱歪みやアンダーカットの無い事はもちろん、後加工を考慮してポイントのみにフィギュアリングを行なわなければなれなかった。
溶接範囲は約8×20mmで、ワーク材質がSTAVAXであった。
(写真13)はフィギュアリング後の写真である。
レーザスポット径をφ0.5mmに設定して、溶接ワイヤーはSTAVAXのφ0.3mmを使用した。
必要部分だけをフィギュアリングし、熱歪みやアンダーカットなどの発生も無かった。 形状が複雑な為に、レーザの照射角度を変更しながら加工を行なった。
また、レーザフィギュアリング特有の同時に焼き入れ効果も得られ、硬度はHRC50であった。
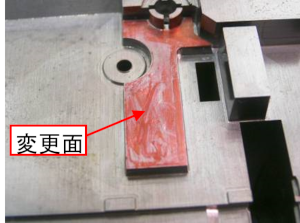
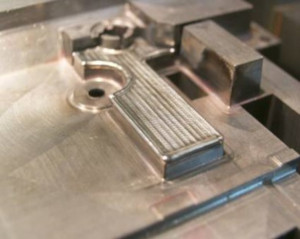
3. 極小部品へのフィギュアリング
(写真14)は電子部品金型のコアピンである。
写真のエッジ部分が磨耗している。
また、型番を変更する為に、文字彫刻を埋めなければならなかった。
コアピンが非常に細く小さい為に、レーザ熱入力に細心の注意を払う必要があった。
ワークはSKH51であった。

(写真15)はフィギュアリング後の写真である。
レーザスポット径をφ0.3mmに設定して、溶接ワイヤーはSKH51のφ0.2mmを使用した。
スポットとワイヤー径を小さくする事により、レーザの熱入力を最小に抑えた。
また、フィギュアリングのスピードもワークの温度上昇を抑える為に、低速で行なった。
結果、反りや歪み、アンダーカットの無いフィギュアリングに成功した。


コアピンの先端をフィギュアリング
(製品材料SKD11 溶接範囲 1.5×2×t=0.2mm)
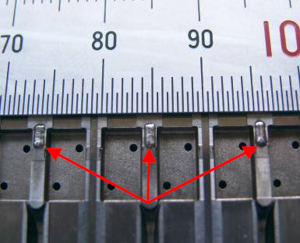
インサート金型の改造
(製品材料SKD11 溶接範囲 1.2×0.7×t=0.3mm)

アルミダイキャスト製品のピンホールをフィギュアリング
(溶接範囲 5×1×t=0.2mm)

銅合金金型のフィギュアリング
(製品材料ベリリウム銅 溶接範囲 4×15×t=0.2mm)
新しい再生技術であるレーザフィギュアリングを必要とする製品は、同じ物を複数加工することが少ない。
様々な製品の様々な箇所にそれぞれの要求に適したフィギュアリングを行なわなければいけない為に、レーザ機には汎用性が必要になり、また加工時の治工具等も豊富に取り揃える必要がある。
レーザ加工機は専用機、自動機として使われることが多く、またそれらがメリットでもあるがこのフィギュアリングで使用した機械は、(写真20)光学顕微鏡を覗きながら、直接ターゲットを目視して、レーザ加工を行なえ、これに治工具を組み合わせて、汎用機として使用することを目的とした。(写真21)
但し、レーザ加工にはレーザ光に対する安全対策が必要不可欠である。
専用ルームに保護具の設置し、作業者はレーザに対する知識や安全教育を熟知していなければならない。
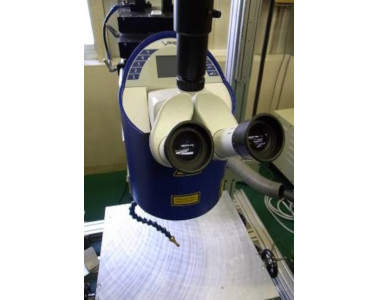
光学顕微鏡が備わった照射ユニット

フィギュアリングの作業風景
まとめ
レーザフィギュアリングの重要ポイント
- 入熱エネルギー量のコントロール
- 加工スピードの調整
- 加工範囲の絞込み
- 使用するレーザスポット径と溶接ワイヤー径の選定
- 照射角度
- 治工具
新しい再生技術であるレーザフィギュアリングは、現在、様々な分野に利用され時間短縮、コスト削減、資源再生など数多くのメリットが有り、今後もこの技術の利用や導入の拡大が予想される。
レーザ加工に関するお問い合わせ・お見積りはこちら
営業時間/8:30-17:30(土日祝除く)